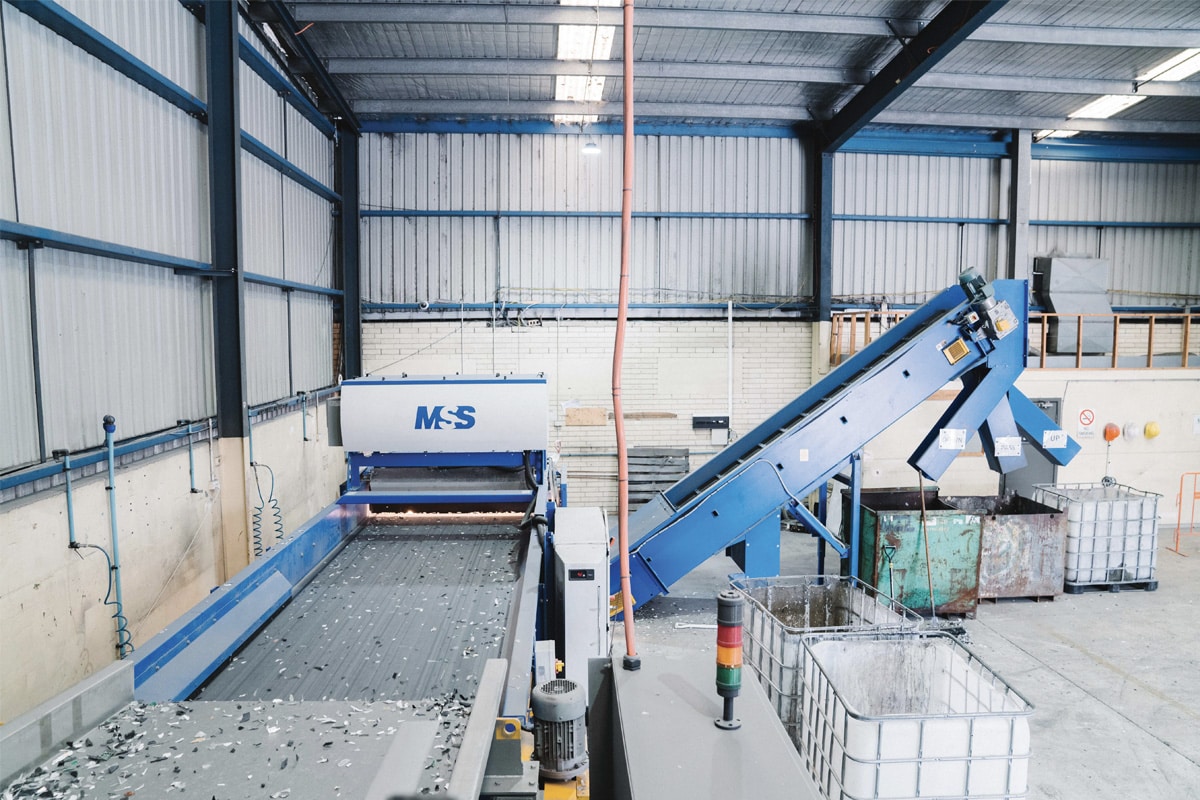
MSS multi-Sensor Sorter
Separating and recovering fractions from hard plastics contained in e-waste to commodity grade is no easy task. However, one company is working on a solution that can help make what has been considered by some, a troublesome waste stream, into reusable raw material.
Chris Sayers is the chief executive officer at Scipher Technologies, a company that believes in the circular economy and is willing to invest in advanced machinery and unique process engineering that will help make sure it plays its role in making it a reality.
The piece of equipment the company has commissioned is called a multi-sensor sorter, which is manufactured in the US by MSS. How does the system work? According to Sayers it uses a number of sensors including a near infra-red based camera placed at the end of the conveyor belt to scan pre-processed fractions according to size, colour, and metal contents. The data is analysed through a series of algorithms that identifies each fraction. This is then fed back through the machine’s computer to drive a series of air-jets located at the end of the conveyor, to separate the different fractions.
“This piece of equipment represents downstream value-add capability to one of our existing processing lines,” he said. “It produces a clean stream of recyclable single-polymer plastic, which is significant in itself, because bonded hard plastics, as opposed to single polymer soft plastic such as PET, is difficult to separate and recover to a grade that is considered exportable, or recyclable. And it’s not just us, it’s our industry compatriots, and e-waste recyclers abroad that are trying to crack the equation here. We’re partway there and we now produce a valuable plastic stream that is exportable”
Sayers said this is just a step for the company in its R&D journey on a solution for e-waste plastics. Currently all mixed recyclable hard plastics are banned from export under federal government legislation that was introduced in July 2021. Scipher Technologies intends to continue its innovative push to invest and develop solutions to separating out further valuable single polymers from mixed bonded hard plastics.
The pre-processing occurs through one of the company’s existing recycling lines, that has been specifically designed
to process TVs, PCs, tablets as well as mobile phones.
“The new equipment is a sophisticated piece of kit and it’s part of our technology strategy, in that we’re not investing into processes that involve the use of chemicals or are energy-intensive. We’re supporting environmentally sound recycling solutions,” said Sayers.
The machine is capable of processing one tonne an hour. Sayers said a typical batch of e-waste contains around 30 per cent by weight mixed bonded hard plastics. Included in this is a range of highly valuable single polymer plastics such as ABS, PP, HIPS and PMMA. PMMA, a unique resin manufactured abroad, is used in flat screen TVs and PC monitors as a glass substitute, otherwise known as acrylic.
“We went through a testing period and we’ve now tuned the equipment and programmed the algorithms to yield specific single-stream products, and one of those is clean PMMA,” he said.
Sourcing feedstock is another issue, but one that Scipher is proactive in addressing. It collaborates with local councils across the country, as well as B2B clients.
“We have direct arrangements with councils in Victoria, NSW and Western Australia,” Sayers said. “We also deal with intermediaries who supply us through their own e-waste collection capabilities.”
As for the end-product, while there is no active market for it in Australia, it is of export quality, said Sayers.
“There are markets in Asia that we’re sending our clean plastic to, where there exists manufacturing capability for electronic equipment,” he said. “We’ve recently programmed the machines to a point where it’s producing export quality outputs – no hazardous elements and 98 per cent plus pure grade.”
One of the considerations when installing a key piece of equipment is making sure there is readily available back-up service from the manufacturer. This is not a problem with the MSS kit.
“The technical support is excellent,” he said. “They’ve online access in real time to help with the performance of the machine. If there’s an issue, we can dial in and the manufacturer can analyse what’s going on.”
While Scipher is currently focused on a solution for separating and recovering hard bonded plastics, the machine is also capable of separating non-ferrous metal fractions. It’s capable of a greater function of tasks from other potential waste input streams, but the company is only focused on e-waste at the moment.
Sayers is happy with how the new equipment is performing, and how Scipher is working on offering a complete solution to a waste stream that, more often than not, ends up in landfill. Keeping these plastics out of landfill means Scipher is not only making sure the environment is being taken care of, but the company is also doing its bit to support a circular economy.
This article originally appeared in the August 2023 issue of Inside Waste.